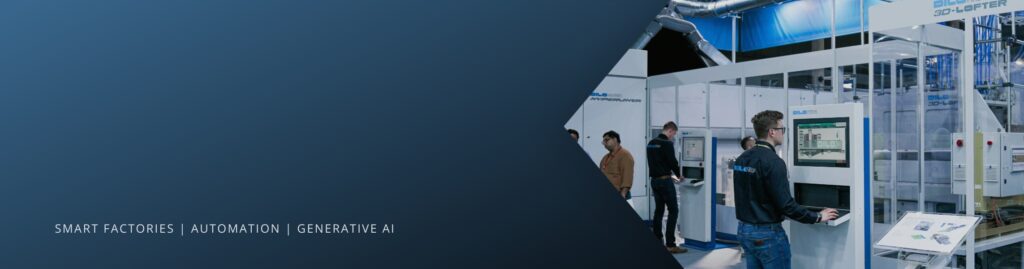
Deep Dive: A Capital Planning Executive’s Perspectives on Trends in the Manufacturing Industry
With 2024 in full swing, here’s a snapshot of the trends manufacturing executives expect will shape the rest of the year.
The continued rise of smart factories
Of the many innovations that characterize Industry 4.0, none are more impactful than smart factories. The emergence of generative AI has linked technologies like the internet of things (IoT), cloud computing, and 5G, melding them into a cohesive whole. Together, they’re ushering in a new generation of factories that harness the data captured by machine sensors to minimize unplanned downtime, improve process efficiency, and even help identify new revenue streams. By and large, experts anticipate smart factories to be a key source of competitive advantage in 2024 and beyond.
Read more: National Association of Manufacturers https://documents.nam.org/MBS/NAM_Trends_2024_WEB.pdf
Our take: While electricity was the fuel that powered manufacturing during the Industrial Revolution, the lifeblood of this new generation of factories is data. Organizations that are able to harness, organize, and make sense of this data will be in an enviable position in 2024 and beyond. For those with a stake in Capex, deep project-level data can now be married with other organizational performance metrics within an active dashboard to vastly improve the ability to budget more wisely and forecast more accurately the outcomes that are determinative of success.
Reshoring for resilience
Whether it’s reshoring, nearshoring, or friendshoring, the shift away from sprawling global supply chains is clear. The pandemic underscored the vulnerabilities of fragile, just-in-time supply chains, catalyzing a movement towards production closer to the end consumer. The transition is well underway; Forbes reports that “69% of U.S. manufacturers have begun reshoring their supply chains, with 94% reporting success in doing so.”
With legislative incentives like the CHIPS Act bolstering this shift, 2024 will see manufacturers increasingly focus on reducing foreign dependencies and enhancing supply chain resilience.
Read more: Forbes https://www.forbes.com/sites/jimvinoski/2024/01/25/covid-is-fading-but-reshoring-isnt/
Our take: The shift from a far-flung global supply chain to a more localized model won’t happen overnight. To ensure that operations aren’t affected during the transition, producers will have to make steady changes rather than major overhauls.
Capex is a key ingredient in this transformation, as significant investments may be required in building new facilities/plants, which may also require shifts in strategies regarding how and where to allocate capital. Doing this well requires a holistic view of all projects that have been planned, started and even completed – which is infinitely easier and more insightful within a purpose-built capital planning tool such as Finario.
Addressing structural labor challenges
Acute labor shortages as a result of the pandemic were a key contributor to the supply chain woes of 2020 and 2021. Since then, most supply chains have adapted, and shortages have subsided.
But while the short-term labor crisis has more or less passed, the long-run picture is still pretty dire. Demographic changes in the workforce, notably the retirement of Baby Boomers, are projected to drive a manufacturing job gap of 2.1 million by 2030. Addressing a shortage of this magnitude will require significant investments in worker training and automation.
Fortunately for producers, advancements in AI and automation are enhancing worker productivity and enabling factories to operate with fewer staff. The adoption of these technologies is crucial for businesses aiming to maintain or elevate production levels despite the dwindling labor force.
Read more: Vention https://vention.io/blogs/2024-industrial-automation-trend-predictions-715
Our take: While AI-powered automation will take on increasingly complex tasks in the coming years, entirely automated factories are a ways away. Skilled workers will still be needed to supervise and operate machines, and making sure they’re trained in how to use the latest technologies will be vital.
As we covered in our article on the topic, given the amount of money at stake, embracing Capex automation is a no-brainer. Common obstacles, including the lack of a transformation champion and a system to track project details, can prevent leaders from prioritizing the technology, but there are ways for Capex stakeholders to counter this. For example, doing some “back of the envelope” calculations to determine the potential impact it can have using tools such as our ROI calculator.
Generative AI enters the factory floor
After being introduced in the 1960s, robotic machinery transformed how factories look, feel, and operate. By relieving humans of heavy lifting and strenuous physical work, they boosted productivity and efficiency on the factory floor.
As generative AI makes its way into manufacturing, it’s drawing many parallels to the robotics era. Rather than replacing workers entirely, it’s providing them with data-driven insights that make them more productive. By analyzing vast datasets and user preferences, it can suggest innovative designs and predict potential performance metrics. This empowers engineers to make informed decisions quickly, freeing them from tedious calculations and guesswork.
Read more: BCG https://www.bcg.com/publications/2023/gen-ai-role-in-factory-of-future
Our take: Generative AI is fueled by data: the more it can ingest and learn from, the more useful it becomes.
Predictive analytics, machine learning and AI are making its way into the corporate finance software stack, and Capex is no exception. Finario, for example, includes tools that can help predict future forecasts based on completed projects that have – utilizing numerous indicators – similar characteristics … as well as continuously analyze capital project performance against benchmarks both internal and external. This can be invaluable in shaping capital programs across time (e.g. today, next quarter, 5-year plan), and from top to bottom (e.g. project, budget, portfolio) more strategically.
New automation technologies reshape manufacturing processes
Along with generative AI, new automation technologies like digital twins and 4D vision are reshaping how many kinds of products are made. Rather than needing to create and tinker with a physical prototype, digital twins enable producers to make design tweaks cheaply and quickly. For instance, a company can create a digital twin of a new assembly line to test and optimize its efficiency before building the physical line. This can help to identify and fix potential problems early in the design process, saving time and money.
Just as digital twins streamline product development, 4D vision is transforming factories by providing machines with human-like perception. This technology employs AI to analyze images from 2D cameras, creating a 3D understanding of the environment. It enables robots to recognize and respond to object orientation and characteristics in real-time, optimizing manufacturing processes without the need for complex hardware. The result is a significant enhancement in efficiency and accuracy, allowing for quicker adaptation and problem solving.
Read more: JR Automation https://www.jrautomation.com/blog/blog/2024/01/04/the-evolution-of-industrial-automation-in-2024
Our take: As with smart factories, producers that quickly implement new automation technologies into their operations will gain a significant leg up on the competition. The ability to rapidly test and refine designs using digital twins and optimize production processes with 4D vision will be a game-changer for many manufacturers.
However, securing approvals for these next-gen technologies can be complex, notably because many of the stakeholders tasked with evaluating them lack the expertise or experience to do so – given how new they are. It’s why it’s so important that any capital investment approval system has the ability to include user-input rationale, ROI and risk metrics, links to background materials and more.
The green manufacturing revolution accelerates
An influx of public and private funds towards electrification and decarbonization is accelerating the shift towards sustainable production. Manufacturers are taking advantage of these incentives by exploring partnerships, investing in low-carbon technologies, and launching specialized verticals for zero-emissions products to align with the surging demand from investors and consumers for greener manufacturing.
Read more: AlphaSense https://www.alpha-sense.com/blog/trends/manufacturing-trends-outlook
Our take: Embracing the green manufacturing revolution is no longer a maybe — it’s a must for manufacturers in 2024. Consumers, investors, and regulators are demanding eco-friendly practices, which presents a unique opportunity for forward-thinking companies to gain a competitive edge.
Investing in green technologies will be pivotal throughout the rest of the 2020s. But there’s a lot for capital allocators to consider besides strategic alignment and high returns, especially around regulatory requirements such as ESG disclosures. Being able to view all relevant project data in one place can help leaders choose and fund projects that will further their green manufacturing aims; moreover, including ESG criteria throughout the budgeting and approval process ensures compliance in that regard.
Cybersecurity remains a top priority
While smart factories are enabling unprecedented efficiency gains, they’re also expanding the potential for cyberattacks. Traditional factory setups were less susceptible to cyberattacks due to isolated systems, but the expanded attack surface of Industry 4.0 creates numerous entry points for hackers. A successful attack could be devastating, shutting down production lines, causing financial losses, and potentially leading to intellectual property theft or data breaches.
To protect against emerging threats, manufacturers need a proactive approach to cybersecurity. This starts with a comprehensive security strategy that identifies vulnerabilities and assigns clear roles for everyone involved. Securing all connected devices and continuously monitoring network activity are crucial steps. Regular employee training on cybersecurity best practices is equally important, as human error can be a significant vulnerability.
Read more: Spiceworks https://www.spiceworks.com/it-security/cyber-risk-management/guest-article/why-smart-manufacturing-needs-smarter-cybersecurity
Our take: The cybersecurity challenges of Industry 4.0 are considerable, and demand significant attention from senior finance and operations executives. Smart factories come with a host of risks, including hackable machines and concerns around AI governance.
To effectively navigate these obstacles, organizations must embrace a holistic strategy that prioritizes data governance and organizational resilience alongside technical defenses. This approach involves regular risk assessments to pinpoint vulnerabilities, implementing state-of-the-art encryption, and fostering a culture of security awareness among all employees.